We are ready for worldwide deburring challenges. Please contact us, use our tool selector or fill out the enquiry form with your detailed application information. After conducting an analysis, we will find or develop a suitable tool solution for you. For demanding applications, we conduct tests at our headquarters in Switzerland or at your facility using test tools. Your advantage? The entire process of finding a solution is provided at no cost to you.
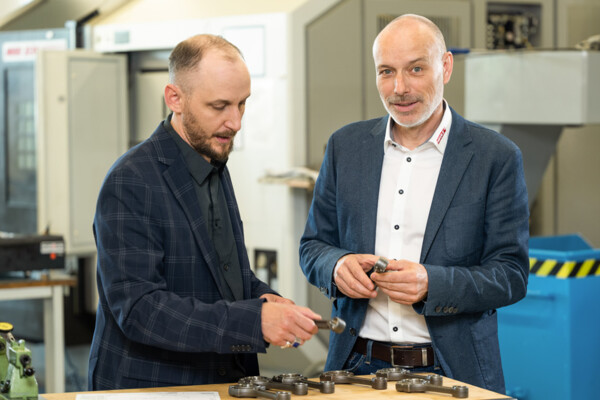